Load-Monitor
A big benefit: Load monitoring system for rail freight.
The loading process is very demanding and time-consuming. Non-optimal load implicates a couple of negative consequences, such as higher costs or even dangerous situations. If the optimum load capacity is not used, i.e. if the wagon is underloaded, this is to the detriment of economic efficiency.
PJM has developed a load monitoring system, which automatically determines and analyses the loading process and the load. Signal lamps or the on-site visualisation on the display immediately indicate the loading situation and so the system assists the loading staff during the loading process and enables an immediate adjustment of the load.
The signal lamps on the wagon indicate:
- Overload
- Wheel set overload
- Wheel disc overload
- Asymmetric load
- Inadmissible bogie load distribution
- Load is ok
- Load level (threshold)
In addition, all the relevant data is available in the web portal. Important information is sent automatically to the person in charge, e.g. when the load limit is exceeded.
The signal lamps indicate up to seven loading situations.

Functionalities at a glance
- The system indicates: load weight, overload, asymmetric load, free load capacity
- Automated determination of: wheel set, wheel disc and overall load for all types of rail freight wagons
- The strain-gauged-based system is highly precise, very reliable, free from wear and long-lasting
- On-site signal lamp providing crucial information to the loading staff, including a switch on and switch off feature
- Encoded, secure connection
- Information in the web portal is available for various user groups
Benefits at a glance
- Optimum load capacity of the rail freight
- Increased safety, due to correct load
- Simplified loading process, due to automated processing
- Optimum use of capacity of the transport fleet
- On-site visualisation
- Real-time data transfer to the web portal
- Long-lasting, wear-free system for the whole range of freight wagons
The load monitor provides safety and an increase in efficiency: Due to relevant information, the load is always at an optimum level (e.g. symmetric load, no overload etc.) and the load capacity is optimum, too. This is a win-win situation: The carriers and logistics companies appreciate cost savings and the environment benefits from less CO² emissions.
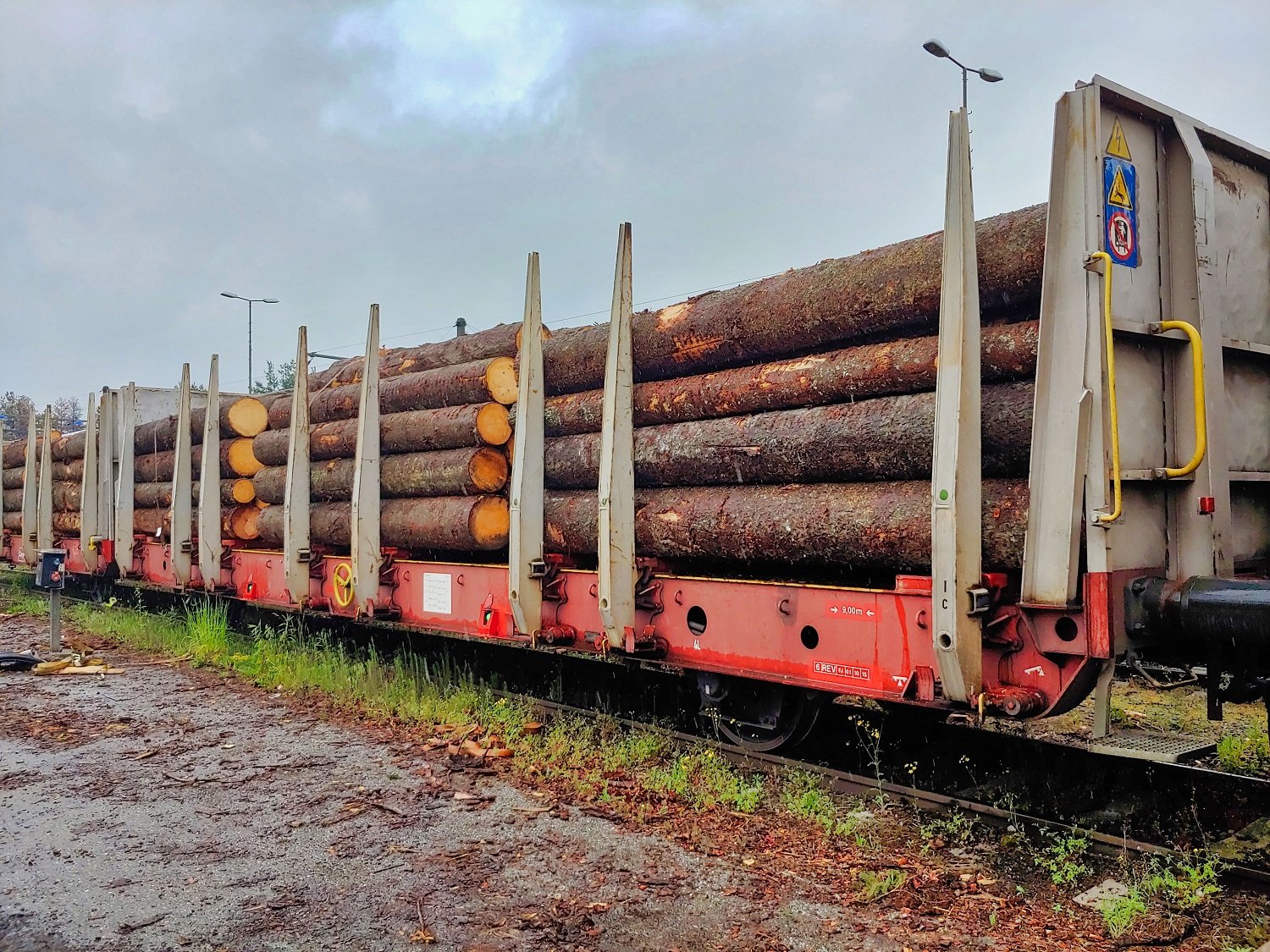
- Time saving: Loading can be carried out faster, as the loading maximum is reached more quickly. Since the wagons no longer exceed the maximum permissible weight, time-consuming separation at infrastructure points is also eliminated. Many companies run additional distances for a separate weighing in order to detect any overloading. In these cases, the time saved can be booked twice (at the additional cost of making these journeys).
- Improved communication: End customers as well as freight forwarders receive important information such as loading progress and shunting times in real-time.
- Reliable data transmission: Data acquisition is precise and convenient. Users thus save time and costs, as there is no more time-consuming fault finding.
- Immediate effects: The automatic monitoring of the loading weight brings immediate positive effects. The significant increase in the factors of system efficiency, safety and cost-effectiveness ensures a rapid ROI effect. Concrete efficiency increases are consistently present, but vary depending on the transport material.
Benefits
The load monitoring system provides safety and creates efficiency: With the help of the relevant information, the load is optimally placed (symmetrical, no overloading) and the loading capacity is used in the best possible way. This results in a double positive effect: The carriers save costs and the environment is pleased about a valuable CO² reduction.
- Optimal utilisation of loading capacity: The on-site visualisation via direct display on the wagon or via app is an important support for the loading personnel during the loading process. Especially with "difficult" loads such as wood, scrap or bulk goods, this is a great relief. Optimally loaded freight wagons are efficient, prevent unnecessary extra journeys and save costs.
- No more overloading: Exceeding the permissible maximum weight is displayed in real time and can be corrected immediately, as can asymmetrical loading. The loading personnel as well as the wagon owner and the logistician have the certainty of an optimal, permissible loading.
- Reduced process flow: Automatic weight detection reduces or completely eliminates manual weighing.
- Paperless administration and thus significantly less possible errors: The wagon lists are provided in a clear, digital form.
- Reduction of wear and repair costs: Since there are no more overloaded wagons, wheel sets and frames are less stressed and thus repairs are reduced or the possible mileage is increased.
- Generally improved repair management: Through the early detection of e.g. flat spots, costly reprofiling with high material removal and possibly follow-up costs are avoided, thus also preventing the particularly expensive downtimes.
Which functionalities are provided by the load monitoring system? What are the benefits?
The proven load monitoring system comprises numerous functionalities and provides a wide range of benefits:
- The wear-free hub generator provides the monitoring system - and further
applications - and is energy self-sufficient.
- The automatic load identification determines changes of the loading weight immediately and turns on and off the signal lamps mounted on the wagon and activates the digital monitoring
system. The system checks the loading situation at specified intervals and is activated automatically when any weight changes occur. In addition, the on-site visualisation is activated
to identify an overload or asymmetric loading and thus assists the loading staff during the loading procedure (this also depends on the type of WaggonTracker system used). It is
not possible to power such an automated system using batteries.
- On account of the simultaneous automatic data transfer into the web portal, the train driver is continuously informed about the loading situation. This facilitates better planning of loading capacity. In addition, the permanent monitoring of load and tonne-kms enables a better planning of maintenance intervals, maintenance stops and components required during the servicing of wagons.
- The WaggonTracker ADV which was designed especially for wagons, determines the loading weight with a strain gauge-system which is maintenance-free and long-lasting. These strain gauges are usually mounted on the bogies. Depending on the WaggonTracker type, between one and four metering points are installed on the bogie frame. The average annual measurement accuracy is about 2.5 % per year.
- The calibration is set in the web portal, and the data is transferred and recorded into the on-site system. Thus, the loading staff can always rely on the full range of functionalities and crucial data such as calibration and loading limits, even without an internet connection.
- The calibration is set in the web portal, and the data is transferred and recorded into the on-site system. Thus, the loading staff can always rely on the full range of functionalities and crucial data such as calibration and loading limits, even without an internet connection.
- In addition, the system also takes into account both summer and winter season conditions, including, for instance, the weight of snow on a wagon. The required data for calibration wagon traverses a calibrated scales. Furthermore, the manufacturer can undertake such a calibration using a bogie pressure-stand.
- The WaggonTracker ADV product range provides reliable information - the status of the running gear, position, direction of travel and ambient temperature are all determined and recorded. In addition, depending on the WaggonTracker requirements, it is possible to determine running safety, and standardised buffing and vertical wheel forces. The system can be upgraded with any necessary requirements.
- The WaggonTracker Standard provides geofencing to automatically determine the maximum permitted loading weight on various parts of route, according to rail infrastructure classifications.

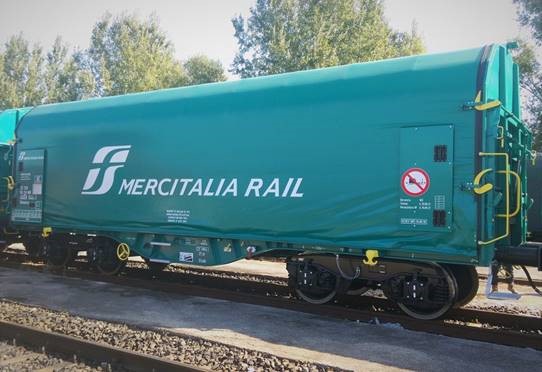
Contact
Felix Egger-Cimenti
More information on Load-Monitor ...
You are interested in further information? Please fill in this form or contact us directly.